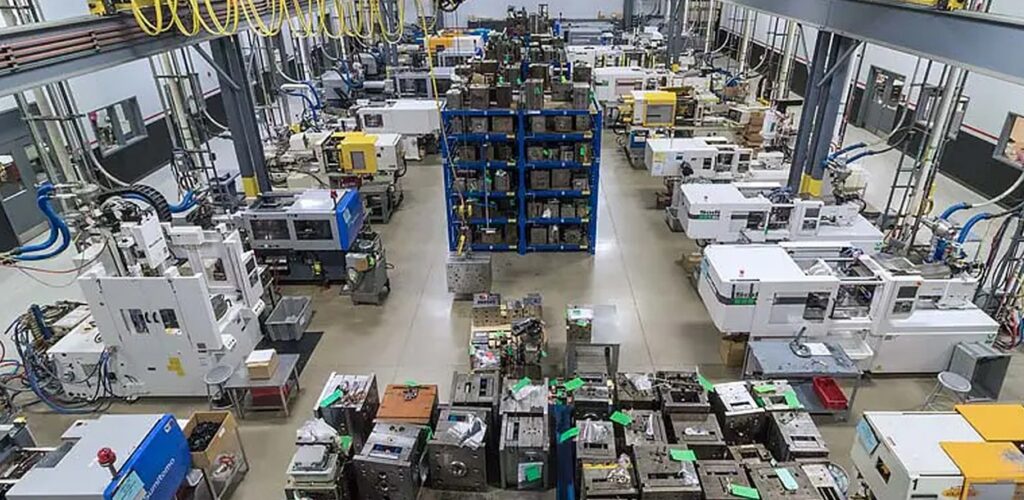
Plastic molding has become an essential component of modern manufacturing, offering incredible versatility across various industries. From everyday household items to complex automotive parts, the process of plastic molding allows manufacturers to create products with precision, consistency, and efficiency. In this article, we’ll explore the wide-ranging applications of plastic mold and the innovative techniques shaping the future of this dynamic field.
What is Plastic Molding?
Plastic molding is a process that involves shaping plastic materials into desired forms using molds. These molds are typically made from metal and can be used to produce thousands, if not millions injection molding companies near me, of identical parts. The process usually involves injecting molten plastic into the mold, allowing it to cool and harden before the part is ejected. The versatility of plastic molding lies in its ability to produce intricate designs with minimal waste and high efficiency.
Types of Plastic Molding Processes
There are several different methods of plastic molding, each suited to specific types of applications and products:
- Injection Molding: This is the most common method, used to create a wide variety of parts by injecting molten plastic into a mold. It’s highly efficient for mass production.
- Blow Molding: Typically used for hollow objects like bottles and containers, blow molding involves inflating a molten tube of plastic into the shape of a mold.
- Compression Molding: This process involves placing a plastic material into an open mold and then compressing it into the desired shape.
- Extrusion Molding: Used for products with a continuous cross-section, such as pipes and sheets, extrusion molding forces plastic through a shaped die.
Applications of Plastic Molding in Modern Manufacturing
Plastic molding has revolutionized numerous industries, enabling manufacturers to produce high-quality products at scale. Some of the key sectors where plastic molding is essential include:
1. Automotive Industry
In the automotive sector, plastic molding is used to create components such as dashboards, bumpers, and interior trim. The precision and durability of molded plastic parts make them ideal for meeting the high-performance requirements of vehicles. Additionally, lightweight plastic components help reduce overall vehicle weight, improving fuel efficiency.
2. Consumer Electronics
From smartphones to laptops, plastic molding plays a critical role in the production of electronic devices. Molded plastic is used for housing components, connectors, and even intricate internal parts. The flexibility of plastic allows manufacturers to create durable, sleek designs that are lightweight yet sturdy.
3. Medical Devices
The medical industry benefits greatly from plastic molding due to its ability to produce sterile, high-precision components. Plastic molds are used to manufacture items such as syringes, IV tubes, and even prosthetic devices. Innovations in bio-compatible plastics have further expanded the role of plastic molding in the medical field.
4. Packaging
Plastic molding is widely used in packaging, particularly for food, beverages, and cosmetics. Blow molding is commonly employed to produce bottles and containers, while injection molding is used for lids, caps, and other packaging elements. Plastic packaging is lightweight, cost-effective, and provides excellent protection for products.
5. Home Appliances
Home appliances such as refrigerators, washing machines, and microwaves often contain numerous plastic-molded parts. The durability and versatility of plastic make it ideal for producing both aesthetic and functional components in household products.
Innovations in Plastic Molding
The field of plastic molding has seen several technological advancements in recent years, leading to more efficient and sustainable manufacturing processes. Some of the most notable innovations include:
1. 3D Printing and Rapid Prototyping
3D printing technology has introduced a new dimension to plastic molding, enabling manufacturers to quickly produce prototypes before committing to large-scale production. This allows for faster product development cycles and more accurate testing of new designs.
2. Eco-friendly Materials
As sustainability becomes a priority in manufacturing, there has been a shift toward using eco-friendly and biodegradable plastics. Innovations in bioplastics and recycled materials are helping reduce the environmental impact of plastic molding, making it a greener option for modern manufacturers.
3. Micro Molding
Micro molding involves creating extremely small plastic components, often for use in medical devices or electronic products. This innovation allows manufacturers to produce highly precise parts with exceptional detail, expanding the possibilities for miniaturized technology.
4. Multi-Material Molding
In multi-material molding, different types of plastics or even other materials are combined to create a single component. This allows manufacturers to produce parts with varied properties, such as flexibility in one section and rigidity in another, all in one process.
Challenges and Future Trends in Plastic Molding
Despite its many advantages, plastic molding also faces challenges. Environmental concerns about plastic waste have led to stricter regulations on plastic production and disposal. Manufacturers are now tasked with finding ways to make the process more sustainable without compromising quality.
In the future, we can expect further innovations in recycling techniques and the development of new, environmentally friendly materials. Additionally, automation and smart manufacturing technologies will likely continue to drive efficiency in plastic molding, reducing costs and waste while improving product quality.
Conclusion
Plastic molding is a cornerstone of modern manufacturing, offering versatility, efficiency, and precision across a wide range of industries. As technological advancements and sustainability efforts continue to shape the field, the future of plastic molding looks promising, with exciting innovations on the horizon. Whether in automotive parts, medical devices, or everyday household items, plastic molding is sure to remain an integral part of the manufacturing world for years to come.